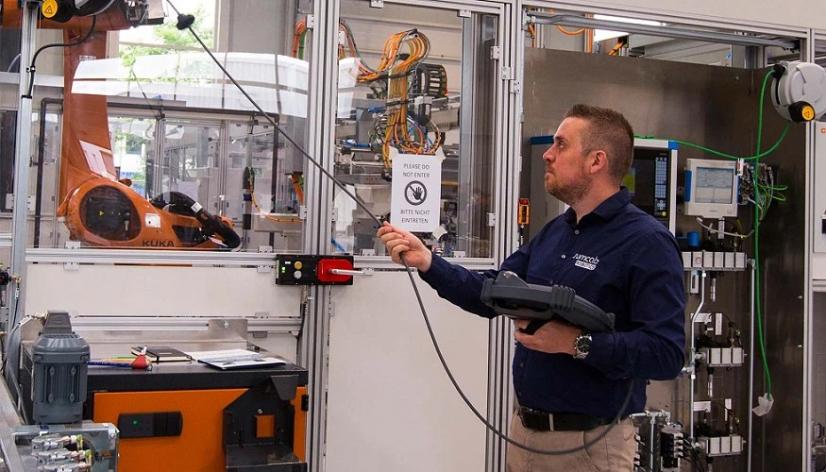
In the automotive industry, industrial robotics plays an essential role in the automation of key processes such as assembly, painting, quality control and others. One of the major challenges in this sector is to ensure the reliability and durability of the components used in automated systems. A recurring problem is premature wear of cables and energy packs, which can cause unexpected production downtimes and affect the quality of the final product.
The problem of cable wear in industrial environments
In many industrial applications, cables used in robotic systems often suffer accelerated degradation due to demanding operating conditions. Despite the use of standard market products and robust energy packs, cables eventually deteriorate after a short service life. This wear not only causes intermittent system failures, but can lead to unplanned production downtime, with serious economic consequences.
Cabling deterioration usually starts with small defects that seem harmless, but as these accumulate, the quality of the final finish of the product is affected. Early identification of degradation is essential, as unplanned downtimes are a factor that any production line seeks to minimise.
Analysis of the situation and proposed solutions
Facing these challenges, Sumcab Robotics’s technical team identifies several key factors that contribute to cable wear in this type of application. Although the selection of a more suitable cable helps to partially improve the situation, it is usually realised that the design of the energy pack was too stiff and incorrectly positioned, forcing the cables to exceed the recommended bend radii. This incorrect positioning increased the mechanical stress on the cabling, accelerating its wear.
In the automotive industry, industrial robotics plays an essential role in the automation of key processes such as assembly, painting, quality control and others. One of the major challenges in this sector is to ensure the reliability and durability of the components used in automated systems. A recurring problem is premature wear of cables and energy packs, which can cause unexpected production downtimes and affect the quality of the final product.
To address this problem, Sumcab's mechanical design team develops custom metal anchors that allow to reposition the tube and its contents, remarkably reducing the aggressiveness in handling the energy pack. This adjustment is key to improving the longevity of the cables and reducing the stresses to which they were subjected.
Optimisation of trajectories and harmony of movement
Even with these improvements, Sumcab's technical team checks the movement system to verify if there is potential for further optimisation. To achieve this, it also involves the programming team to assess the system's trajectories. In many cases, collaboration between technicians and programmers results in the optimisation of robot trajectories, which not only reduces mechanical stress on the cables but also improves system cycle times, having a positive impact on productivity.
Robotic integration standards: a new approach
As a result of these developments, production lines take a new approach to robot integration, including Sumcab’s participation from the initial design stages. This allows full adaptation of the systems to the requirements of the environment and specific applications, remarkably improving the efficiency and lifetime of the components. In addition, other production lines are readapted to implement the standard developed by Sumcab Robotics, ensuring greater reliability in the systems while optimising production times at all levels.
Conclusion
The implementation of custom solutions in cable selection, energy pack design and trajectory optimisation can make a significant difference to the durability and efficiency of robotic systems. Sumcab Robotics has proved that a holistic and collaborative approach, from design to programming, is key to solving recurring problems in production line maintenance and ensuring operational continuity in complex industrial environments such as the automotive industry.