
Fully automatic robot-assisted online measurement systems are often used for quality control purposes in production processes. However, the rapid movements made by these robots often lead to wear and tear on parts of the installation. In the particular case of standard corrugated tube cable packages, the supply of both power and communications to/from the measurement camera is exposed to strong abrasion and must therefore be replaced frequently.
In the automotive industry, processes to check the finish on vehicle bodywork are essential for guaranteeing production quality. Groove dimensions are examined during these processes to ensure uniformity using online measurement technology (IMT), for which a component is examined from all sides and from various angles via robot-mounted cameras. This is a complex task in which the robot guidance system, the camera and the analysis software must all work in perfect unison.
Several companies have specialised in offering solutions for this type of automatic measurement technology on production lines. For their clients, which mainly operate in the automotive sector, the speed with which a component can be checked is paramount. The speed of the testing process has a direct impact on production capacity and, by extension, production costs. To enable a short cycle time while also ensuring entirely reliable control of the component, the speed and degree of movement offered by the measurement robot must be fully harnessed.
Challenge: combating power supply wear and tear incidents
Nonetheless, no matter how good the solution is, it will only be able to function correctly if proper communications and power supply to the camera is guaranteed via high-strength cabling. This cable needs to withstand the tension produced by the rapid position changes by the camera and the complex trajectory guide for the robotic arm. Standard energy packages are used for this purpose, which consist of corrugated tubes protecting the cable from abrasion damage. However, faults continue to occur because the corrugated tubes themselves are exposed to high levels of wear and tear due to the formation of loops and significant abrasion.
To combat this situation, IMT manufacturers seek an optimised solution for energy packages that can guarantee a better alternative for powering cables and thereby avoiding downtime on production lines.
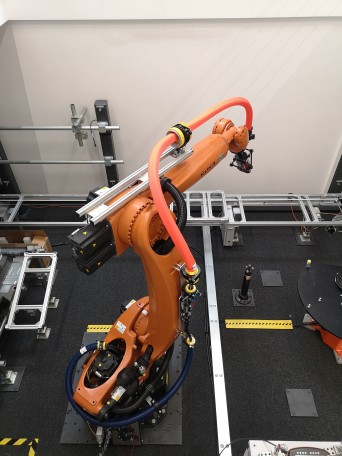
Solution: Sumotex guarantees optimised power supply
In response to this challenge, Sumcab Robotics has developed Sumotex, a system in which the cable packages are no longer contained within a corrugated tube but rather a high-tech air-filled textile housing. This is an entirely innovative dresspack solution based on a set of pressure chambers assisted by in-built pneumatics. Thanks to the high-strength and highly adaptable textile covering, Sumotex can work with the right air pressure without losing flexibility while maintaining the necessary rigidity for the work being done by the robot.
This prevents rubbing, enables greater flexibility of movement and, thanks to the compressed air system that runs through the interior, gives it airbag-like protection against potential impact from welds, hot parts or the abrasion caused by friction with the robot chassis itself.
Furthermore, in order to maximise adaptation to the needs of the client, Sumotex is always designed following a prior study of the movements made by the robot on which it will be installed. This fully optimises the solution proposed and avoids unscheduled downtime. We develop the entire solution; in short: the metal fittings, rotation systems and necessary guidance systems to accompany robotic movement in all operations.
The systems is also extremely easy to install and has an excellent design that can be adapted to any medium or large industrial robot, guaranteeing an optimised power supply to the various tools being used by the robot. Furthermore, it always uses certified cables for industrial robotics and the design enables the repair or replacement of system parts without needing to switch out the whole assembly.
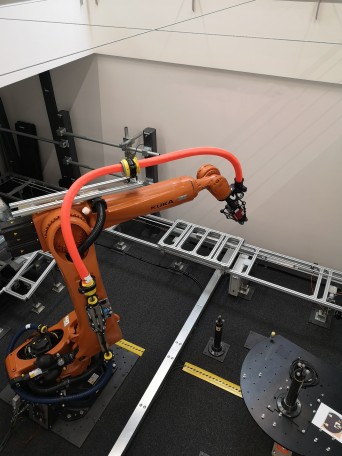
With Sumotex, IMT measurement technology providers can offer their customers a new and significantly more reliable solution for their to-camera power supply. The new system enables faster robot movements and, therefore, a higher frequency of cycles in the checking operation.
Sumotex’s various applications in online measurement technology are already operating successfully. The results are excellent: the service life of the Sumotex energy package is significantly longer than that of conventional packages. This ensures a safe and trouble-free measurement process. And reducing maintenance times increases the production capacity of the manufacturing line.
In just over a year from its launch, many customers are already benefiting from the advantages of Sumotex, especially those who have robots assigned to tasks such as guiding material to tools, vision systems or handling processes.
If you want to know about all our dresspack solutions, pay us a visit.